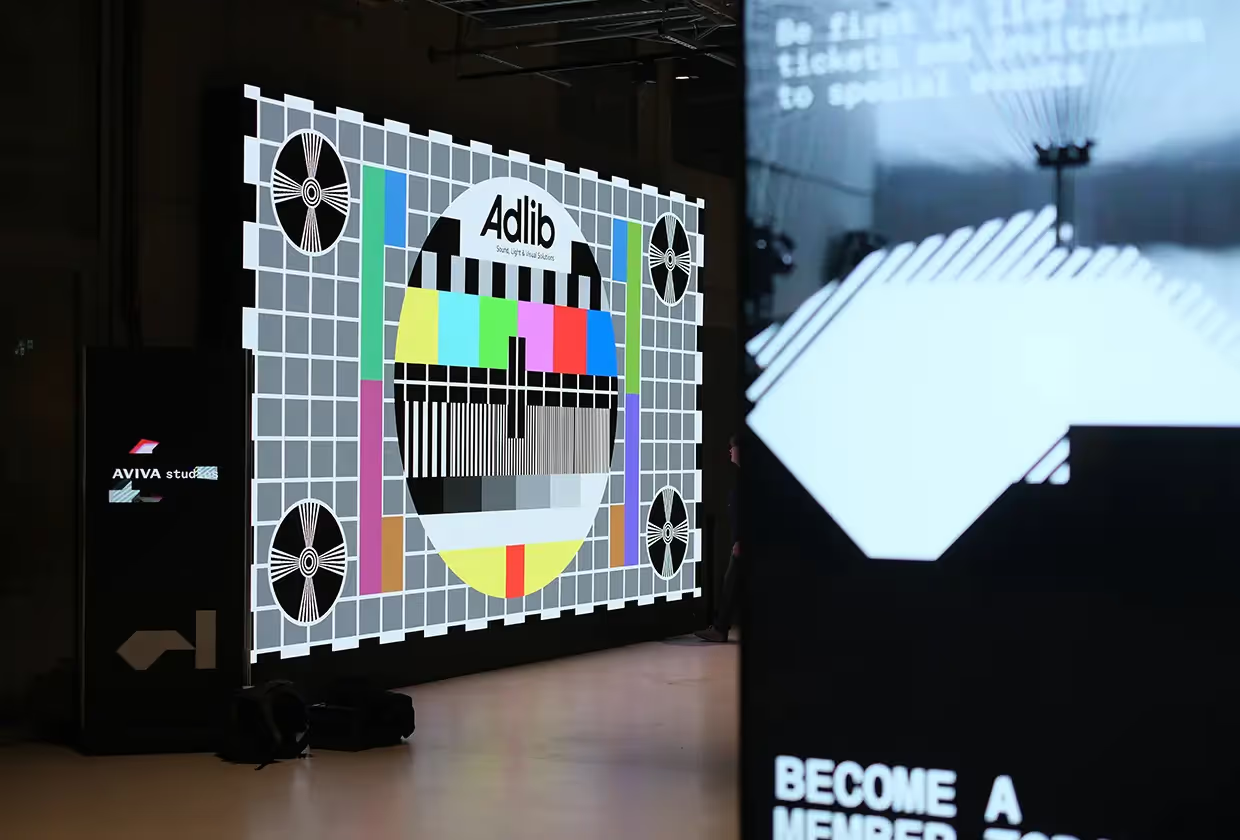
Overview
Landmark cultural space opens in Manchester with seemingly limitless production possibilities, redefining what it means to be multipurpose.
Partners & Collaborators
Client
Aviva Studios
Sector
Live Venues
Services
Location
Manchester, United Kingdom
Year
This article originally appeared in issue #34.1 of MONDO DR, which you can read here.
Arguably the most exciting new creative space to open in the UK in several years, Aviva Studios, home of Factory International, has been built and equipped with flexibility in mind.
Factory International is the organisation behind both Manchester International Festival (MIF), and the new venue, and it commissions, produces and presents an ambitious year-round programme of original creative work across the spectrum of music, performance, visual arts and popular culture, and special events at its new venue, online, and internationally, as well as staging the citywide festival every other year. Located in the St John’s neighbourhood to the west of the city of Manchester, Aviva Studios is based around large, open, adaptable spaces that can be constantly reconfigured to suit artistic needs.
The 13,350 sq m building features two performance spaces that work together. The 21m-high Warehouse has a capacity for up to 5,000 people (standing), which can be divided by two movable, full-height acoustic walls to create two separate spaces, while the Hall is a flexible auditorium, which can hold 1,603 seated or 2,000 standing. The proscenium in the Hall can fully open into the Warehouse, allowing its stage to run deep into the Warehouse.
The design of the building was led by architectural firm Office for Metropolitan Architecture (OMA), with several vendors brought in to ensure its technological requirements were met.
“The ethos behind the venue is artist flexibility,” said Paul Moore, Factory International Director of Production and Operations. “It is an amazing space to reconfigure and explore all of its possibilities, and it is a testament to our industry how well all the different vendors and contractors involved in this project worked together to deliver it.” After winning the tender process to provide theatre consultancy for the venue, Charcoalblue was pivotal in bringing the building’s inspiring artistic vision to life, resulting in a ground-breaking new theatre typology: an arts warehouse.
Several specialist companies worked with the venue staff, and often with each other across the various technological elements within the building. These included J&C Joel, White Light (WL) - a d&b Solutions company, Adlib, Solotech, Unusual Rigging and Torpedo Factory Group. Charcoalblue brought in local stage engineering firm J&C Joel to deliver the steelwork across the two performance spaces.
“In many ways, we make the building work from a theatrical point of view – there’s the building shell, and we provide the equipment that makes it work as a theatre or performance venue,” said Conor McGivern, Special Projects Manager, J&C Joel. “For an iconic and ground-breaking project of this size there had to be a constant dialogue with the main contractors to ensure a successful delivery, because unless the equipment we provide is installed successfully and works, it won’t function as a theatre.”
McGivern and his team delivered multiple elements across both performance spaces, including ensuring a safe working environment in the Hall’s production grid area with handrails, access gates and a drawbridge, 12 additional beam trolleys, technical towers on either side for extra rigging points for lighting and sound equipment, stage rostra and fascia, and an orchestra pit elevator.
The stage area can be adapted so that the space can be used as a seating area, and so J&C Joel installed a flexible HOAC rostra system, which can be set up to create various different staging scenarios, ranging from flat floor, stage level to a traditional theatre seating layout with orchestra pit. The orchestra pit lift was designed and installed using SERAPID rigid chain technology and can be set at four levels.
“It’s a four-chain SERAPID pit lift,” confirmed McGivern. “SERAPID offers the best of any of the pit lifts available because they’re reliable, very accurate and relatively easy to assemble.” Above the Warehouse, a number of A-frame grid stands were designed and supplied to enable a wide range of rigging points, and strong points were added to the walls to allow for a variety of equipment to be fixed, including technical equipment bars, circus equipment, seating structures or bespoke scenic elements.
One custom solution that had to be developed is two uniquely designed travelling trollies which run the length of the underside of the Warehouse grid, each equipped with a
2-tonne chain hoist for the transport of heavy equipment from one end of the room to the other.
“Our challenge here was to make a hoist that kept moving across the gap created to facilitate the operation of the two sliding doors which separate the room in two, without losing power from one end, and without stopping,” said McGivern. “It was a complex design, and the team did a brilliant job because the hoist had to ‘jump’ that gap.”
SERAPID technology was also utilised by Suffolk-based firm ESP in the dual 40m length HGV lifts which operate on one side of the venue, and having two lifts is a massive benefit to the venue according to Moore. “They are fantastic and one of them has straight line access from the lift directly into the Warehouse, which can quicken turnaround,” he said. “They are also located adjacent to the Hall, which can help facilitate an easier load-in.”
The venue’s Global Control System (GCS) for the automation was delivered by Unusual Rigging as it was awarded the role by building constructors Laing O’Rourke. After many discussions with the Factory International team, given the uniqueness of the space, a design and supply of equipment was finalised. “In addition to the GCS, we realised that there was a need for a ‘theatre style’ flying solution and consequently developed a new five-line winch system (Revolution 2) for the main Warehouse space, designed, fabricated and delivered specifically for this project,” said Mike Goodwin, Capital Projects Manager, Unusual Rigging. “All the hoists, winches, load cells, and rigging that went into the venue – the totality of the rigging hardware – was examined and supplied to cover as many use cases as can currently be envisioned for the technicians in the Warehouse and Hall.”
The global control system encompasses a TAIT Navigator system, controlled by epi-Q desks, as the operator’s interface, whilst the ‘brains’ of the system sits in a server in the grid-level control room where the central controller NAV.RS4 units are located.
“Over 200 LiftKet single-speed chain hoists and 19 vary-speed Kinesys apexHOISTs were supplied, in addition to the new concept five-line winches,” Goodwin revealed. “Whilst there was a collaboration with J&C Joel on the grid stands at grid level with some testing in our facility using some of their equipment, the overall package of automation for the venue was principally a collaboration between Unusual Rigging, Kinesys and Push the Button, developed and installed according to the Laing O’Rourke stage engineering contract and Charcoalblue’s specification, integrated into the base build containment infrastructure.” Inside the Warehouse, Moore explained its concept: “There is a lot of scope to change the room for different purposes,” he said. “It is dividable in two with movable walls that can be slotted into place, which were built by Dutch company MultiWal. They have two functions because in addition to dividing the Warehouse, they act as acoustic absorption. They work on rollers and give us flexibility – for example, a show can be worked on in one space while a production is being held in the other.”
Another element that enhances the venue is the purchase of a selection of ModTruss, a modular aluminium beam which can be set up in a manner of ways, developed by Triple E, as well as an amount of its metric, steel successor BEEEM, which is much stronger.
“We built a 10m by 10m span room with the BEEEM, which people walked through and acted as a viewing platform during the Yayoi Kusama exhibition held in the Warehouse over summer,” said Moore. “It can also be utilised to build a temporary bar for larger concerts in the Warehouse space, and act as an accessibility viewing platform. We’ve had a lot of support from Triple E as we learn its full capabilities. From a sustainability point of view, we can unbolt it, take it down and store it away when it’s not required, which negates the need for us to rent a similar setup, saving time and carbon emissions. It’s a fantastic product.”
Lucy Edelstein, Managing Director, Triple E & EEE Build, is delighted to see the company’s products used in such a prestigious new venue. “Working on the opening of the Aviva Studios with Paul and their team was a wonderful experience,” she reflected. “The ideas and motivation behind their work is inspirational and I can’t wait to see what they produce in the coming years and how they put our fantastic modular structural solutions to good use.” When it came to lighting and remote power solutions for the venue, Moore and his colleague Jack Thompson, Associate Technical Director, Factory International, collaborated closely with White Light (WL) - a d&b Solutions company, to ensure that the right equipment was selected and within budget.
Antony Vine, Key Account Manager (Sales) at White Light, recalled the process. “Our collaboration went through a number of iterations as we traversed the pandemic, and once we were awarded the contract, we worked closely together to engineer our way to an equipment spec that worked for them against a fixed budget and a backdrop of increases that happened over the pandemic timeframe,” said Vine.
The FOH lighting rig in the Hall is made up of ETC Lustr Series 3 profile fixtures, permanently rigged alongside four ETC High End Halcyon Platinum moving heads, to give the room ample coverage for a theatrical setting.
In addition, 60 ETC High End Halcyon Titanium are carried as stock, to be used by the venue when required. Also supplied were two MA Lighting grandMA3 light control desks, 56 Astera AX9 Battery Pars and over 100 additional LED generics and moving heads. White Light also oversaw the supply of a zactrack Pro tracking system and power distribution unit from StageSmarts. The zactrack, Astera and MA Lighting equipment was delivered via UK distributors Ambersphere with WL.
“The venue is very much in a ‘learning’ phase as it opens and makes its way through the first few months of operation, getting to understand how the equipment works in the venue, so they intentionally didn’t purchase too much before knowing exactly what was needed,” said Vine.
“Because many of the productions that the venue will host will bring in their own equipment, our task was to supply equipment that we knew would cover the most necessary bases as the venue and team found their feet.
“It was a privilege to work alongside Paul and Jack on the project, and that relationship is ongoing as we continue to assist them during the opening, helping with any further purchases required to their inventory as the building’s uses become apparent and the show programming is finalised,” concluded Vine.
Three StageSmarts C72 Racks were purchased through White Light to provide the venue’s mobile power distribution, which gives venue staff monitored data in real time for the power used across certain parts of the venue’s rig.
For Moore, the zactrack investment was an important one for the venue as it can also be inputted into the sound system in the Hall, which is a d&b audiotechnik Soundscape system as supplied and installed by Solotech. “We invested in zactrack PRO as part of the lighting package, but it can also be used as part of the d&b Soundscape system in addition for as its conventional follow-spot function, and that gave it the edge over other tracking solutions,” said Moore. “It can also receive input from the automation desk and be informed when the lighting bar is moved so it tracks the position of the light and the performer via different inputs.”
Back in 2016 in the very early stages of the project, d&b audiotechnik was approached by Charcoalblue to design a flexible system for the Hall, that could be deployed as desired, across the diverse programme that Factory International produces.
After winning the contract, Solotech was then brought onboard to deliver the sound system, with Adam Hockley, Business Development Manager d&b audiotechnik serving as the project lead for d&b, collaborating with Richard Burgess at Charcoalblue, Phil Aitken, Kieran Edmonds and Kyle Durno at Solotech, and Moore and Thompson from Factory International.
“After looking at the technical specs for the audio system over a period of time and ironing out the requirements of the venue, we signed off on a design in August 2022 and went into purchasing mode the following month,” said Phil Aitken, Sales Executive, Solotech. “The d&b Soundscape system encompasses five main line array hangs across the main truss with 60 speakers on the walls. The total number of sound sources is 128, and so with Soundscape the sound can be placed from anywhere in the venue.
“From our perspective, this is a really interesting install as it is a surround sound system designed to correspond with the visual elements on the stage, rather than a simple task of hanging speakers at one end of a room.”
Moore added: “Because we are artist-led, the incoming sound designer can configure this sound system to their liking. There are 60 of the d&b 8S speakers installed around the walls to create the 360° sound and E6 speakers underneath the balcony front. It’s a permanent setup, but the hanging arrays can be adapted or added to if a production requires.”
The venue’s entire professional audio package was supplied by Solotech, encompassing DiGiCo Quantum 338 and Quantum 225 desks for control, Shure Axient wireless microphone system, Clear-Com FreeSpeak II communications system, and the cabling and flight cases for storage.
Also installed is a sound system for the area of the venue known as the Social, where visitors gather ahead of a show or exhibition to enjoy some refreshments, with a variety of Martin Audio loudspeakers supplied to be configured to cater to the room’s needs. Signal distribution here is handled by a Q-Sys 110f core processor.
Additionally situated in the Social, is a 6m wide Ultra-HD INFiLED WP Pro 2.5 screen which can be used for a variety of applications pending on how the room is being used including digital artwork, signage or as the backdrop to a pop-up live events stage. This was provided by Adlib who supplied the venue’s video infrastructure.
“Adlib worked across four different areas of the project,” said Ashley Ball, Video Technical Manager, “this encompassed digital signage – both fixed and movable, multiple LED wall installations, guest and performer entertainment solutions in the back of house areas, the supply of video equipment packages and network-based video distribution infrastructure throughout the venue.” To meet the brief for the digital signage and the back of house entertainment packages, a selection of 34 Panasonic displays were installed across the venue, accompanied by 30 BrightSign players. Also supplied for deployment by the in-house technical team were ready to go portable packages of Panasonic PT-RQ25 4K projectors and Panasonic AW-UE150 PTZ cameras.
“The biggest area of focus for Adlib while we were pitching ideas to the venue was to deliver a video distribution system to link up the production spaces with the capacity to achieve UHD resolutions anywhere in the venue,” continued Ball. “We designed and installed an all-encompassing infrastructure system, which as far as we are aware is the first deployment of this kind of technology permanently installed in a live entertainment venue in the UK.” Torpedo Factory Group installed SDI infrastructure throughout the venue, and Adlib designed and configured a 300Gb/s ST2110 media network using Nvidia switches to facilitate this - expanding and extending the capability of the building’s SDI cabling.
“We designed an enclosure for the Riedel MediorNet IP FusioN which connects to fibre facility panels located throughout the building and provides a variety of video input and outputs to allow the technical team to work with an array of equipment which production or touring artists bring into the venue,” said Ball. “The enclosures can be plugged anywhere into the network and connected with the other 74 ST2110 video endpoints in the building hosted in Riedel’s VirtU frames populated with MuoN IO SFPs. They can all be controlled via a tablet or web interface to direct video sources to any area of the building as needed, such as a projector, screen, display or a destination of their choice.”
Andrew Watts, Head of Technical, Adlib, was involved in selecting the Riedel MediorNet IP having previously worked with ST2110 networks in broadcast projects.
“This type of technology is now starting to enter the live events space, and we worked closely with Riedel to see how we can make this product work in venues,” said Watts. “It is a very flexible system which is essential due to the broad nature of events that this venue can host, we didn’t want to restrict the production team in the long term.
“Elements of the system can be redeployed in the building to suit their needs, and at the time the products were specified no shows had taken place, so being able to pre-empt those needs would have been impossible. The hyper-modular design meant that we are giving them longevity and not making presumptions that might be incorrect.” Torpedo Factory Group provided a Blackmagic Design ATEM 2 M/E Constellation HD which is utilised for show relay and distribution, and a show relay monitor is situated in the rack, with Adlib adding a ‘live events’ layer of equipment for vision mixing, recording solutions and live streaming along with 4K links into digital signage and screens in the building. Assisted listening across the venue is delivered via a Williams AV Wavecast Eight, which supplies eight channels that can be assigned across different parts of the building, and anyone connected to the Wi-Fi can receive it, while a paging system for the back of house area is powered by Yamaha XMV8140-D amplifiers.
None of the above would be possible without the technical infrastructure backbone conceptualised and designed by Charcoalblue, a future-proofed blank canvas from which to create the unimaginable.
The venue first welcomed visitors to the Warehouse when it held a huge Yayoi Kusama exhibition in summer as part of MIF. Aviva Studios officially opened in October with the production of Free Your Mind, directed by Danny Boyle, running for three weeks, and Moore is quick to emphasise that the marriage of technology and talent is important for a performance space as complex as this.
Factory International launched Factory Academy in 2018 with the vision of training the creative workforce of the future, and a lot of the technological choices that went into the venue were made with this in mind. A Technical Trainer will be employed directly by Factory International to deliver venue-based training, providing a pipeline for technical roles at a range of levels at Aviva Studios and across the region.
“Factory Academy is really important to us as that has an emphasis on introducing new entrants into this field,” said Moore. “We have been working with the Executive team to create opportunities across our departments – the artisans and technicians – to learn and develop. Initially, it is about us getting to grips with the venue and the technology, but then it will move on to be about innovation and progressing people’s careers.
“For me, the best asset of the building is our team of operators. We have an amazing team, and when they all have full confidence and knowledge of how all the different systems and technologies can be utilised, it will be a very exciting time.”
Credits